Yes, you can splice an ABS sensor wire. This type of repair requires a soldering iron and heat shrink tubing to make the connections secure and watertight. First, cut the damaged section out of the wiring harness with scissors or a knife.
Then strip back both ends of each wire about one inch. Twist together each pair of wires (be sure to match up positive with positive and negative with negative). Now it’s time to solder your connection, ensuring that there is good contact between both sets of wires.
Finally, cover your newly-formed joint in heat shrink tubing for extra protection from corrosion and other environmental elements. With this method you can splice an ABS sensor wire safely and effectively!
- Prepare the Wire – Cut and strip both ends of the ABS sensor wire to expose approximately 1/2 inch of bare copper wiring
- Make sure that each end is cut straight and smooth before proceeding with splicing
- Twist Both Wires Together – Using a pair of needle-nose pliers, twist together the two exposed wires until they are securely connected in one single piece
- It is important to ensure that all strands are intertwined properly for an adequate connection between the two wires
- Solder Joints – Apply heat from a soldering iron or gun to both sides of the twisted joint, while simultaneously applying solder directly onto it until there is enough material surrounding the joint for a secure connection; allow it time to cool down before proceeding further with your project
- 4
- Wrap Electrical Tape Around Spliced Area – Once cooled down, wrap electrical tape around both ends of the spliced area for added protection against any possible short circuit or loss in current flow caused by external elements such as moisture; this will also improve performance and reliability over time if maintained regularly
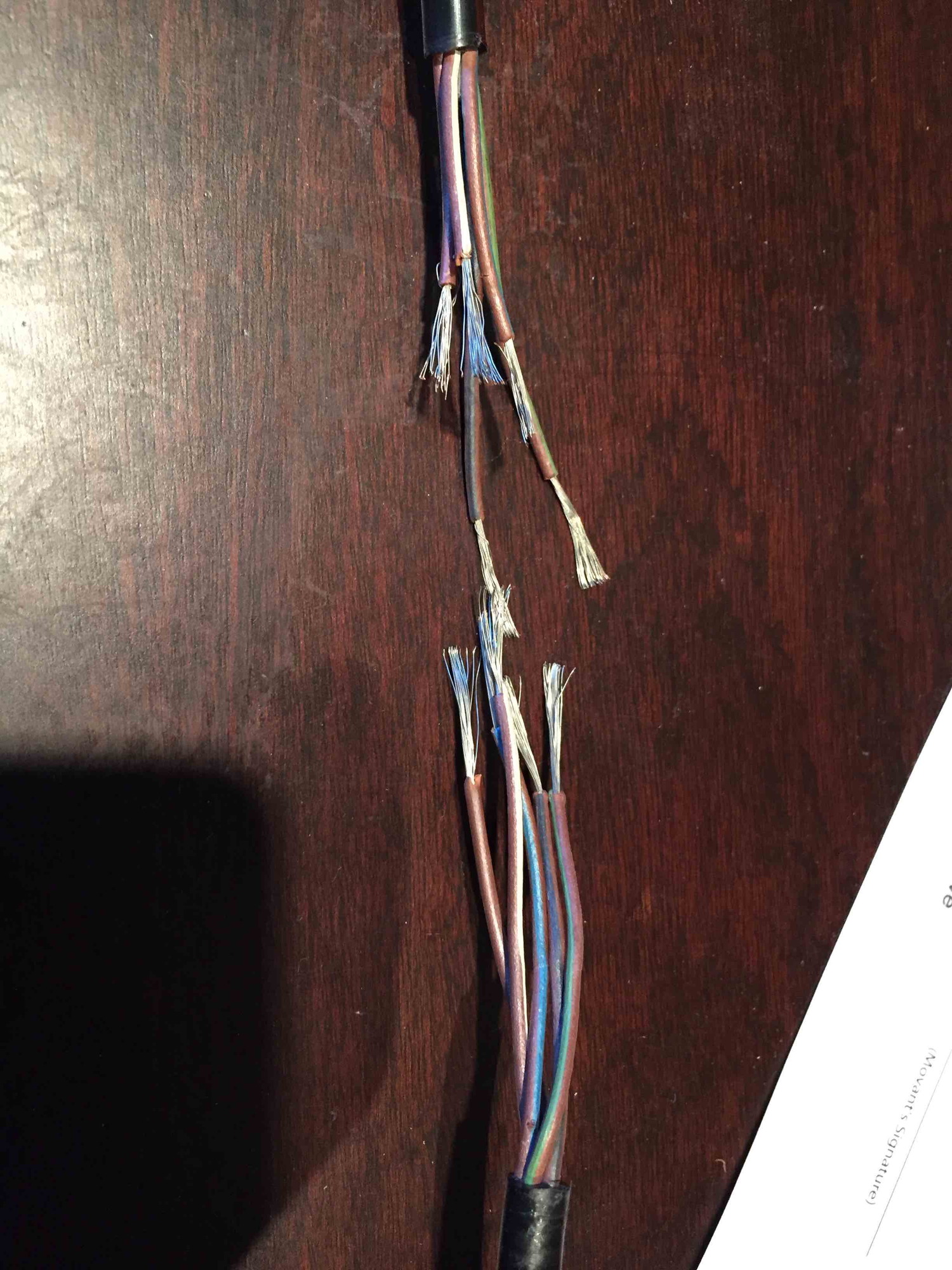
Credit: rennlist.com
Can You Solder Wheel Speed Sensor Wires?
Yes, it is possible to solder wheel speed sensor wires. It requires careful preparation and attention to detail in order to ensure that the connection is strong and secure. When soldering a wheel speed sensor wire, you will need some basic tools like pliers, tweezers, a soldering iron with appropriate tips for your project and electrical grade solder.
Additionally, make sure that there are no other objects touching the area of contact between the two wires as this can cause interference or an unsafe connection once complete. Once all of these items are present, begin by stripping away any insulation from around each end of both wires before tinning them with your soldering iron and solder paste for improved conductivity. After this has been done correctly on both ends of the wires being joined together, use your soldering iron to heat up each joint until melted enough for a secure connection before allowing it time to cool down completely prior to testing its integrity with an appropriate multimeter reading device.
Following these steps should guarantee successful soldering of wheel speed sensor wires every time!
How Many Wires Does an Abs Sensor Have?
An Anti-lock Brake System (ABS) sensor is a critical component of any vehicle’s braking system. It monitors the speed of each wheel and sends information to the ABS controller so it can apply or release pressure on individual brakes as needed. Generally, an ABS sensor has three wires: one for power, one for ground, and one signal wire that transmits data back to the ECU.
The signal wire will vary in size depending on the type of sensor being used; some have smaller gauge wiring while others have larger gauge wiring. Additionally, some vehicles may also use additional sensors with four or five wires instead of just three.
Do Abs Wires Need to Be Twisted?
ABS (Acrylonitrile Butadiene Styrene) wires are often used in many applications, including automotive and industrial wiring. When working with ABS wires, one important consideration is whether or not they need to be twisted. The answer depends on the application and type of wire being used.
In general, twisting ABS wires is not necessary as long as the insulation meets the proper specifications for temperature and abrasion resistance. However, if an extra layer of protection is desired then it may be beneficial to twist the individual conductors together to reduce electrical noise from outside sources such as motors or other nearby equipment. Additionally, depending on the environment that these wires will be operating in, additional shielding or plastic coverings may also be required for added protection against external elements like moisture or dust particles which could cause corrosion over time.
Ultimately it is best to consult a professional electrician or engineer when deciding whether twisting your ABS wire is necessary for your specific application in order to ensure safety and optimal performance over its lifetime.
What Gauge Wire is Abs Wire?
When it comes to wiring, it can be confusing trying to determine which type of wire is best for a given application. ABS (Acrylonitrile Butadiene Styrene) is one of the most common types of wires used in residential and commercial applications. ABS wire has many advantages over other types of wires due to its durable construction and excellent electrical properties.
When discussing what gauge wire is recommended for use with ABS, there are several factors that should be taken into consideration. In general, an 18-gauge solid core copper or aluminum conductor should be used when wiring with ABS. This size offers plenty of flexibility while providing good current carrying capacity and resistance against shorting out during installation or operation.
Additionally, some applications may require larger sizes such as 14-gauge if higher current needs are required.
Easily and Simply Extend your Jeep Wrangler ABS Wheel Speed Sensor Wiring
How to Repair Abs Sensor Wire
If your ABS sensor wire is damaged, it can be repaired with a few simple steps. Begin by unplugging the existing wire from both the wheel speed sensor and ECU. Then cut away any damage in the cable sheath, being careful not to nick or break the wires inside.
Once exposed, inspect each individual conductor wire for signs of wear or corrosion and replace if necessary. After that, use electrical tape to re-insulate any bare wiring before wrapping with insulation tape to reinforce the repair. Finally plug back into both sensors and ECU and test for proper operation of your ABS system.
Conclusion
In conclusion, splicing an ABS sensor wire is not a difficult task if you have the right tools and know how to do it properly. It requires patience and caution as any mistakes can cause serious damage to your vehicle’s electrical systems. However, with proper instruction and practice, splicing an ABS sensor wire can be done successfully in no time at all.