Self-calibration is a procedure that can be used for aligning equipment. Alignment procedures are critical to ensure optimal performance of machinery and equipment.
Traditionally, calibration is done manually, which can be time-consuming and error-prone. However, with the advent of automated self-calibration techniques, many alignment procedures can be done quickly and efficiently without requiring extensive training or specialized equipment. Self-calibration can be used to align various types of machinery, including optical systems, positioning equipment, and precision measurement tools. By using self-calibration, operators can quickly and accurately align equipment, reducing downtime and increasing productivity. Additionally, self-calibration reduces the need for external calibration services, saving time and money over the long term. As a result, self-calibration has become an increasingly popular technique for equipment alignment across various industries.
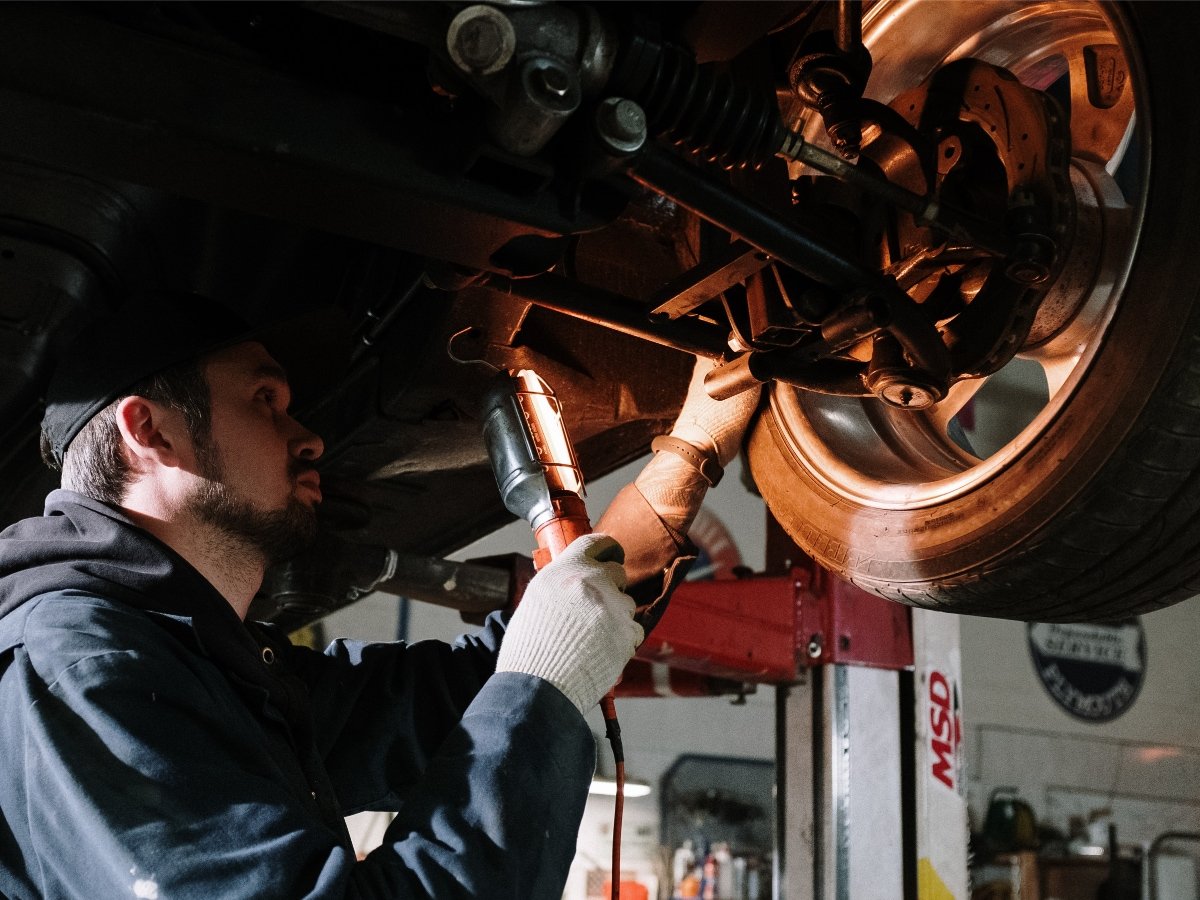
Credit: www.jdpower.com
Understanding Calibration Processes
Calibration is the process of comparing a measurement device or an instrument’s output to a standard. It ensures that measurements are accurate, precise, and reliable. Calibration is crucial in various industries such as medical, manufacturing, and aviation. Inaccuracy in measurement can lead to severe consequences.
There are different types of calibration processes, including in-house, on-site, and self-calibration. Self-calibration, also known as automatic calibration, is a newer approach that uses embedded sensors to perform the calibration process. It offers several benefits, such as reduced downtime, increased efficiency, and cost savings.
With self-calibration, users can achieve optimal accuracy and maintain their instruments without relying on external resources. Overall, understanding calibration processes is essential for ensuring high-quality measurements and reducing the risk of errors.
Benefits Of Self-Calibration
Self-calibration is a cost-effective alignment procedure that optimises accuracy, saves time, and improves productivity. With this method, alignment tasks can be done with minimal supervision, reducing the need for expert personnel. Self-calibration aligns machines automatically by using sensors, software, and algorithms to create a feedback system.
This system adjusts the machines until they meet the predefined specifications, providing a high degree of accuracy. Additionally, self-calibration eliminates the need for manual adjustments, streamlining the entire alignment process and ensuring consistency throughout the system. Moreover, self-calibration ensures machines work correctly, reducing downtime and increasing productivity.
With its numerous advantages in mind, it is easy to see why many industries are investing in this highly effective alignment method.
Fargo HDP Alignment Self Test Calibration
How Self-Calibration Works
Self-calibration systems are becoming increasingly popular in the mechanical engineering industry due to their convenience and accuracy. These systems are used for a variety of alignment procedures, making them a valuable tool for engineers. To find relevant self-calibration systems, research different companies and their offerings.
Once you have found a suitable system, setting it up and operating it is relatively simple. It is important to consider factors such as temperature and vibration when using self-calibration systems to ensure accurate results. By utilizing self-calibration systems, engineers can save time and increase efficiency in their alignment procedures.
Importance Of Proper Alignment Procedures
Proper alignment procedures are essential to ensure that equipment runs smoothly and accurately. Improper alignment can cause significant damage to the machine and lead to risks that could result in costly repairs or even replacement. When equipment is not calibrated correctly, it can cause issues such as misalignment, vibration, and premature wear and tear.
These issues can lead to production downtime and a decrease in product quality. However, self-calibration procedures can help reduce alignment errors by automating the calibration process, leading to greater accuracy and minimizing the risk of human error. It is crucial to implement proper alignment procedures and utilize self-calibration technology to ensure that equipment runs smoothly, increase productivity and prevent costly downtime.
Comparing Self-Calibration To Traditional Calibration Methods
Self-calibration is a convenient way to align equipment for various industries. Compared to traditional calibration methods, it is cost-effective. This is especially true for businesses with tight budgets. Quality assurance and accuracy of self-calibration have their advantages and disadvantages. In instances where extreme accuracy is required, traditional methods are preferred.
Nonetheless, self-calibration ensures that equipment is within permissible tolerance levels. This eliminates the need for frequent adjustments as equipment is already functioning at optimal levels. Despite the fact that self-calibration may not replace traditional calibration methods completely, it is a great way of maintaining equipment.
Additionally, industries can save a considerable amount of time and money.
Frequently Asked Questions Of Which Alignment Procedure May Be Done Using Self-Calibration
1. What Is Self-Calibration And How Does It Work For Alignment Procedures?
Self-calibration is an advanced technique where a device automatically adjusts itself to an ideal state without the need for external calibration tools. By using internal sensors, algorithms, and calculations, it establishes the ideal state of a device to improve its performance and accuracy in alignment procedures.
2. Are All Alignment Procedures Suitable For Self-Calibration?
No, not all alignment procedures can be self-calibrated. The alignment procedure must have internal sensors that detect deviations from the ideal state and the required algorithms to adjust the device’s position or direction in real-time. It also depends on the device’s accuracy and precision required in the alignment process.
3. What Are The Benefits Of Using Self-Calibration For Alignment Procedures?
Using self-calibration in alignment procedures eliminates the need for external calibration tools, saves time and resources, increases accuracy, and minimizes errors. It also improves the productivity and efficiency of the alignment process by automating the calibration process, reducing human intervention, and providing real-time adjustments.
Conclusion
To align a machine or vehicle, the self-calibration procedure has made the job more effortless and less time-consuming. It’s the best option for those who don’t want to spend money on professional calibration services and prefer to diy. Laser, camera-based, and gps-guided systems are the three types of self-calibration systems currently available in the market.
Each of them has their pros and cons, and their effectiveness depends on the type of machine being calibrated. However, before proceeding with any of these systems, it’s always better to examine the manufacturer’s instruction manual and become thoroughly familiar with the specific type of equipment used for the calibration process.
Self-calibration provides an efficient way to align machines, however, it’s always essential to ensure the self-calibrated equipment properly and thoroughly tested before using them for their intended purpose.