To drill out rotor screws, use a drill with a metal bit and apply steady pressure until the screw releases. Ensure proper safety gear and techniques.
Drilling out rotor screws can be a crucial step in brake maintenance or rotor replacement. These screws often become rusted or stripped, making them difficult to remove with conventional tools. Using a drill offers a straightforward solution to this common issue.
Always choose the correct drill bit size to avoid damaging the rotor. Wear safety goggles and gloves to protect yourself from metal shavings. Proper preparation and technique can make the process smoother and safer. Follow these steps to ensure you can successfully drill out rotor screws without causing further damage to your vehicle’s braking system.
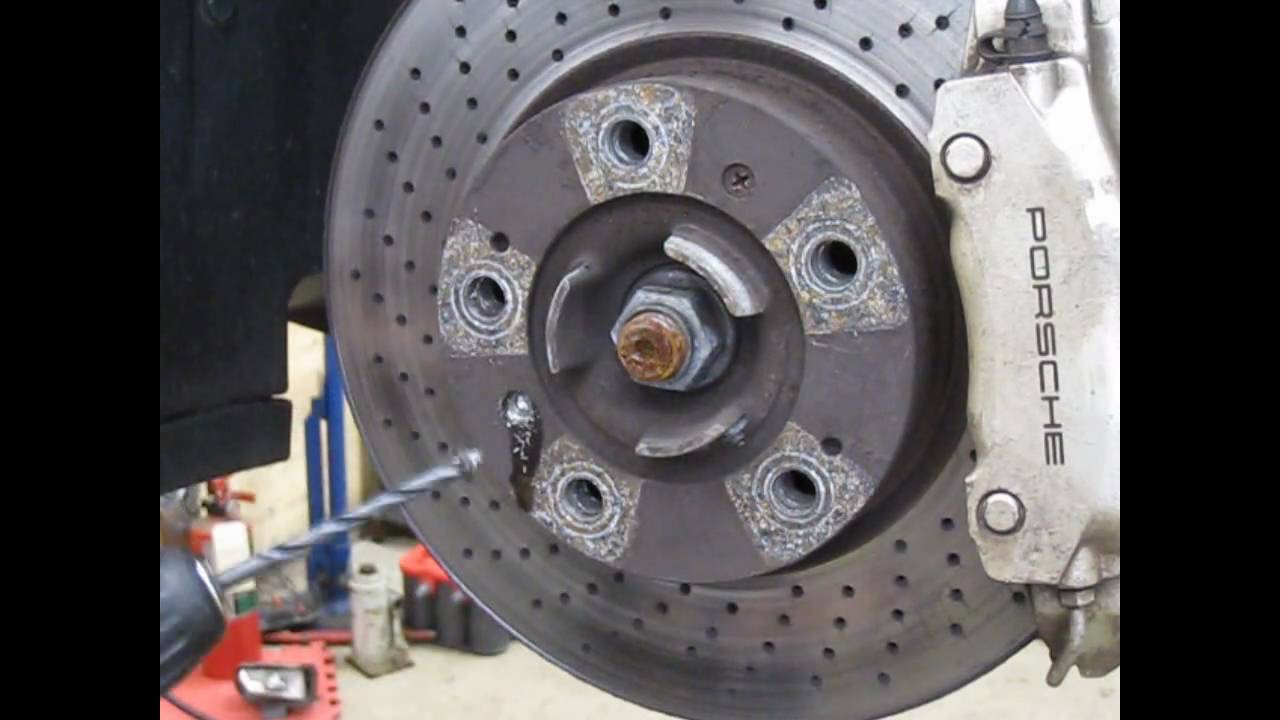
Credit: m.youtube.com
Introduction To Rotor Screws
Rotor screws are small but important parts in vehicle brake systems. They hold the brake rotor in place on the wheel hub. These screws ensure the rotor does not move when you apply the brakes. Without them, the brake rotor might shift. This can lead to serious braking issues and even accidents.
Rotor screws keep the brake rotor steady. They are essential for safe driving. If they are missing or loose, the brake system may not work properly. This can cause dangerous situations on the road. Always check the rotor screws during vehicle maintenance.
Removing rotor screws can be very challenging. The screws often become rusty and stuck over time. This makes them hard to remove. Using a drill is sometimes necessary to get them out. Be careful not to damage the rotor while drilling.

Credit: discoweb.org
Tools And Materials Needed
Essential tools include a power drill, drill bits, and a screw extractor kit. Key materials are penetrating oil, a hammer, and safety glasses.
List Of Essential Tools
A drill is needed to remove rotor screws. Get a drill bit set for different screw sizes. A center punch helps to mark the drilling spot. Use a hammer to tap the center punch. Safety goggles protect your eyes. Wear gloves to keep your hands safe. A screw extractor can be very useful. Have a magnetic tray to hold screws. A flashlight helps to see clearly.
Safety Gear And Precautions
Always wear safety goggles to protect your eyes. Use gloves to keep your hands safe. Make sure the area is well-lit. Keep a first aid kit nearby. Check your tools before using them. Make sure the drill is in good condition. Work in a clean and safe space. Keep children and pets away from the work area. Double-check that the power is off before starting.
Preparation Steps Before Drilling
Ensure you have the correct tools before drilling out rotor screws. Secure the vehicle and clean the area to prevent debris. Mark the screw location for precision.
Cleaning The Screw Area
Clean the screw area using a wire brush. This removes dirt and rust. Wipe the area with a clean cloth to remove loose particles. Ensure the area is clean before proceeding.
Applying Penetrating Oil
Apply penetrating oil to the screw. Let it sit for 15 minutes. The oil loosens the screw. Reapply the oil if needed. Wipe excess oil before drilling.
Choosing The Right Drill Bit
Pick a drill bit that matches the screw size. Use a bit that is just a bit smaller than the screw. This helps in making the right hole size. Always have a few different sizes ready. Test the bit on a scrap piece first. This can save you time and effort.
Cobalt bits are very strong. They work well on hard metals. Titanium bits stay sharp for a long time. Both types last longer than regular bits. They make drilling easier and faster. Less heat is produced, which helps keep the bit sharp. Investing in quality bits can save you money in the long run.
Drilling Technique For Rotor Screws
Begin by choosing a small drill bit. This will create a pilot hole. The pilot hole helps guide the larger drill bits. Make sure to align the drill with the screw center. Apply steady pressure as you drill. The pilot hole should be straight and centered. This step is crucial to prevent slipping. It also helps in the next drilling steps.
After the pilot hole is made, switch to a larger drill bit. Gradually increase the drill bit size. This will make the hole larger step by step. Avoid jumping to a very large bit immediately. Use incremental sizes to ensure control. Each increase should be small and careful. This technique reduces the risk of damaging the rotor. Continue until the screw is drilled out.
Extracting The Screw After Drilling
Removing rotor screws involves precise drilling techniques. Secure the area, then drill the screw head carefully to avoid damage. Use appropriate tools for efficient extraction.
Using A Screw Extractor
Screw extractors are tools that help remove broken screws. First, choose the right extractor size. Insert the extractor into the drilled hole. Turn it counterclockwise. The screw should start to turn out. If it does not, apply a bit more pressure. Be careful not to break the extractor.
Alternative Methods If Extractor Fails
If the extractor fails, try using pliers. Grip the screw head with the pliers. Turn it slowly counterclockwise. If the screw is still stuck, use a hammer and chisel. Tap the chisel gently on the screw head. This can help to loosen it.
Post-drilling Procedures
Ensuring rotor screws are drilled out properly is crucial for brake maintenance. Use a center punch to mark the screw’s center. Apply steady pressure with a drill bit to remove the screws effectively.
Cleaning The Rotor Surface
Remove all debris from the rotor surface. Use a clean cloth for this task. Ensure no metal shavings remain on the surface. A clean surface is crucial for proper function. Apply brake cleaner to the rotor. This will help remove any oil or grease. Wipe the surface thoroughly after applying the cleaner.
Inspecting For Damage
Check the rotor for any visible damage. Look for cracks or deep scratches. Examine the drilled holes closely. Make sure they are smooth and even. Feel the surface with your fingers. It should be smooth to the touch. If you find any damage, consider replacing the rotor. Safety is important when dealing with brakes.

Credit: www.reddit.com
Replacing Rotor Screws
Choose screws that match your rotor. Check the manual for the right size. Stainless steel screws are rust-resistant. They last longer. Do not use screws that are too long. They can damage the rotor. Shorter screws might not hold well. Always use the correct type for safety.
Use a torque wrench for accurate tightening. Set the torque to the recommended value. Do not overtighten the screws. It can strip the threads. Under-tightening can cause the rotor to loosen. Tighten screws in a star pattern. This ensures even pressure. Check each screw after tightening. They should all be secure.
Tips To Avoid Future Rotor Screw Seizure
Anti-seize compounds help prevent screws from sticking. These compounds are easy to apply. Just spread a small amount on the screw threads. This creates a barrier against rust and corrosion. It also makes future removal easier. Use a brush or your fingers to apply it.
Regular maintenance can save you time and money. Check your rotor screws every few months. Make sure they are not rusted or stuck. If you see any rust, clean it off right away. Apply anti-seize compound again if needed. This will keep the screws in good condition. Always use the right tools for the job.
Frequently Asked Questions
How To Get Screws Out Of A Rotor?
Use an impact driver to loosen screws. Apply penetrating oil if screws are stuck. Use a screwdriver to remove them.
Can You Drill Holes In Rotors?
Yes, you can drill holes in rotors. This process is known as cross-drilling. It helps improve braking performance.
How To Drill Out A Brake Disc Bolt?
To drill out a brake disc bolt, use a center punch to mark the bolt center. Drill a pilot hole, then use a larger drill bit to remove the bolt. Apply steady pressure and ensure the drill bit is sharp.
What Kind Of Drill Bit For Drilling Out A Screw?
Use a left-hand drill bit to remove a screw. It grips and extracts the screw effectively. Select a bit slightly smaller than the screw’s head. Apply steady pressure and drill slowly for best results.
Conclusion
Drilling out rotor screws might seem daunting, but with the right tools and steps, it’s manageable. Always ensure safety first. Follow the process carefully to avoid damage. Regular maintenance can prevent future issues. With these tips, you’ll handle rotor screws like a pro.
Happy drilling and maintaining your vehicle!